How to Achieve Burr Free Laser Cutting
- Steven Glassner
- Oct 15, 2019
- 3 min read
Picture this scenario:
You are offloading a sheet of cut parts from the laser machine. From all these pieces, you will pick up a few pieces to reveal clean edges for the next step. And you leave the rest of the pieces with the burred finish.
In order to avoid such burred finishes, you need to know which parameters you exactly need to work on. Here are some handful of strategies to help you get the burr-free prints the way you want.
What Causes Burr?
During the process of laser cutting, the laser beam’s intense energy brings the metal beyond its melting temperature, and the powerful action of the assist gas leaves the metal from the kerf. When you use nitrogen, the cutting process relies on the beam’s energy to melt the metal. When carbon steel is cut, the oxygen interacts with the hot metal for an exothermic reaction. And that adds extra heat.
This is why you don’t need as much gas pressure to eject the material. With oxygen cutting, you have much lower pressure and slower dynamic flow of the gas. Overall, these burrs form from the molten metal solidifying faster than its evacuation. The solid material becomes a deposit at the bottom of the kerf. You can also control the burr by using the right nozzles, Mitsubishi spare parts, and Fanuc spare parts.
The Gas Dynamic
When it comes to nitrogen assist gas, operators need to make changes with quality, efficiency, and costs in mind. It can make up to 35 to 50 percent of the variable cost in laser cutting. Hence, it is important to control the overall consumption. When you set up cutting parameters, it is important to minimize the nozzle diameter. It is also essential to choose the smallest nozzle diameter that you can use to achieve the anticipated quality and performance.
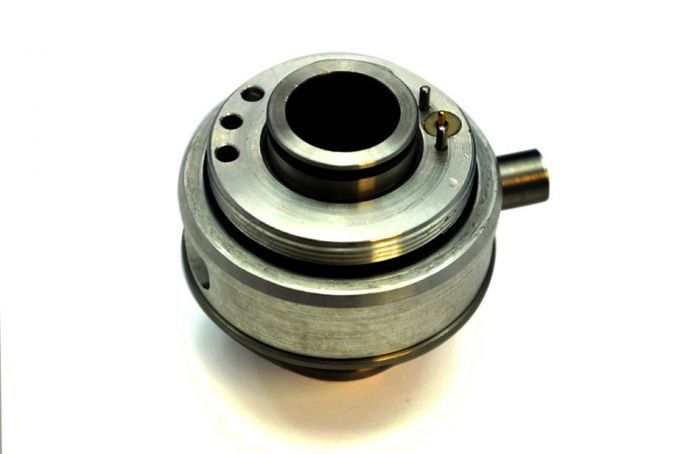
After determining the smallest nozzle diameter, you need to determine the lowest possible pressure to obtain a quality cut with good molten metal separation with no burrs.
It is not the Speed
A burr-free finish is not something achievable with nozzle diameter and gas pressure. You also have to pay attention to the spare parts you are using. Make sure they are either Mitsubishi spare parts or Fanuc spare parts. Additionally, when you go too slowly, you might end up injecting more heat than needed in the kerf. And this might end up raising the temperature to an extreme level. Eventually, it causes vaporization which disturbs the gas flow
That disturbance, in turn, causes more burrs, not less. This means that an operator can make cut quality worse by slowing the feed rate.
You can prevent such events by increasing the cutting speed incrementally.
Consider Oxygen Cuts
When it comes to oxygen cutting for carbon steel, consider the exothermic reaction. It is a fact that with both CO2 and fiber lasers when you increase oxygen global purity to 99.95 percent or above, you can increase the cutting speed in production. Sometimes between 30 to 40 percent.
When an oxygen vacuum flask or cylinder has a drop in purity level, it is usually argon. It happens because the oxygen gets produced cryogenically in an air-separation unit, both oxygen and argon liquefy at similar temperatures.
When you add argon into it, it changes the exothermic reactions. It, in turn, affect the cutting performance. The exothermic reaction works in conjunction with the gas flow rate to burn and evacuate the molten material. If the molten material and oxidized slag aren’t removed effectively, it remains as a burr on the cut edge.
At last pumping
In most laser cutting systems, installers know to avoid elbows in the gas plumbing or to oversize the piping diameter to compensate for pressure drops. With downtime and gas not flowing to the laser, air penetrates and fills the pipe. It can cause problems when the laser is restarted for the next shift or operation.
Final Words!
In order to achieve the burr-free cut, the beam parameters and gas dynamics should work together to ensure the right amount of molten metal evacuates the kerf at the prime time.
Comments