How to Avoid Top Four Mistakes in Laser Engraving
- Steven Glassner
- Jul 28, 2020
- 4 min read
Learning to perfect the use of design equipment is important in order to avoid the mistakes regardless of your position in your career. It’s important to learn the art of perfection.
From time to time, there are issues that leave designers questioning about where they went wrong or finding the way they can better the skills. This pattern of thinking is in each and every creative field even in laser engraving.
If you know the correct ways, you can avoid small mistakes and are less likely to make them again. So, let’s see the top four mistakes laser engravers make and ways to overcome them:
1. Avoid Burning Fabrics
As a laser engraver, you must understand your fabrics. You need to know what type of laser engraving machines you should use, make sure it has high-quality parts like Amada parts and bystronic spare parts, and how much heat the fabrics can handle. Fabrics such as denim, canvas and leather can withstand high power settings during laser engraving. But, with delicate fabrics, it’s necessary to reset the settings keeping high speed i.e. near 100% and low power at 5% to 10%.
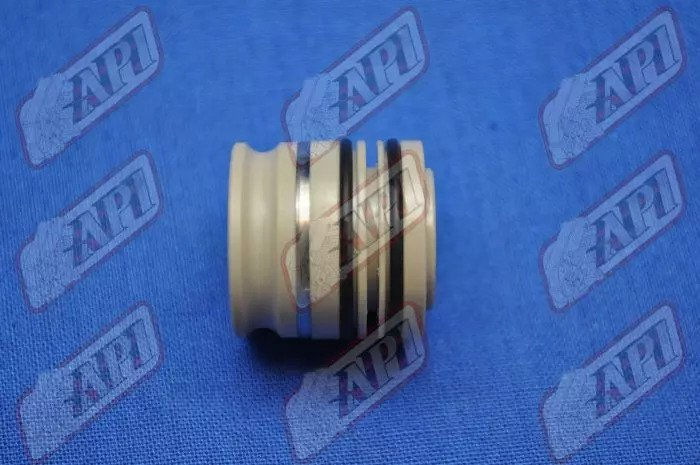
Test these initial settings on some extra materials and if the fabric can withstand it then increase the heat power until you get the output you are looking for. When you work with direct-to-garment engraving, it is necessary to lower the dots per inch at which you engrave. The higher the DPI, the more it removes material. While if you engrave at low DPI it helps to ensure that the laser slightly vaporizes the top layer and doesn’t burn entirely through the fabric. Most fabric engravings are perfect at 150 to 300 DPI.
2. Acrylic Produces White Laser
Two types of acrylics are useful in laser engraving and both have different applications. First, there are cast acrylic sheets. Its objects are of liquid acrylic that it pours into a mold and then you can set them into various shapes and sizes. This type of acrylic is perfect for engraving as it turns a frosty white color making it suitable for awards and plaques. You can cut the fabric with a laser, but it does not give projects flame-polished edges.
Extruded acrylic is the other type of acrylic; it forms into sheets by machines. It is less expensive than cast acrylic because it is made through a high-volume manufacturing technique. However, it reacts differently to the laser engraving machine. This type of acrylic cuts cleanly and smoothly and produces a flame-polished edge. But when you engrave, it does not produce a frosted look, instead provides clear engraving. Hence, as a fabricator, you need to make sure that you are using correct acrylic depending on your requirements.
3. Imperfect Glass Engraving
Usually, when a laser comes in contact with glass, it breaks the surface but does not engrave it deeply or removes the material needed to engrave fully. The breakable glass surface will produce a frosted appearance, but this can be rough and chip depending on the type of glass you use to engrave.
Additionally, it also depends on the type of laser machine you use and parts it has like Amada parts and bystronic spare parts.
Here, are some of the tips you should follow to produce better, smooth glass:
Use low resolution i.e. around 300 DPI which produces better results on the glass as you separate the dots you engrave.
Change the amount of black texture in your graphic to 80 percent.
If possible apply a thin, wet sheet of newspaper or a paper towel to the engraving area. This will help you with heat dissipation and improve the engraving process. Just make sure that there are no wrinkles in the paper which you apply.
Another way to make the heat disappear is to apply a thin coat of liquid dish soap over the area you are engraving using your finger or a paper towel.
Lastly, if there are fragments of glass after you engrave, polish the area using a non-scratch scour pad.
4. Wood Engraving
Wood is one of the most laser friendly materials because we can cut and engrave easily. Usually, different woods have different ways of reacting when we engrave them with lasers and produce different results. Lighter woods like cherry or maple can produce a nice contrast where the laser burns away the wood. Whereas, with the denser woods requires more laser power to cut or engrave.
Grain density can change dramatically depending on the type of wood you are using. Cherry, alder, walnut, and maple have fairly small veins of grains in them and oak has medium to large veins.
Final Words:
As a fabricator, it is very easy to make mistakes and suffer loss because of it. But, I am sure after reading how to solve these four mistakes you will come to know what are the things which create these issues and better your skill. Make sure that you know what type of laser engraving machines you should use and if they have the right parts like Amada parts and bystronic spare parts as these things do matter and affect the quality of the outcome.
Comments