Laser Cutting: Tips and Practical Processes that Work!
- Steven Glassner
- Aug 21, 2020
- 3 min read
Laser cutting is becoming popular in the manufacturing industry. It has even paved its way in industries such as medical, aerospace, electronics, automotive, etc. Its uses and benefits even caught the attention of the education sector and small business enterprises apart from the industrial sector.
Laser cutting has its various advantages to offer like higher edge quality, faster speed, less noise of the equipment and so on. The laser machinery by manufacturers like Prima Optics Laser, Fanuc Parts, etc. provides a comprehensive product range with all these advantages.
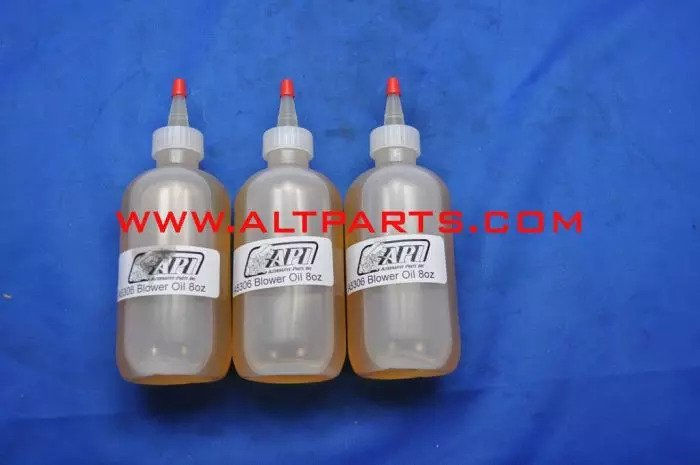
It is necessary to keep a check on the efficiency of the cutting process to avail these benefits to the highest extent.
Discover the tips to improve laser cutting efficiency.
Reduce the Cutting Head Lift
Generally, after working on one profile, the machine will lift to a certain height and then move to the next profile. This prevents the collision with the cut pieces. By optimizing the cutting path, you will be able to reduce the cutting head lift and this, in turn, will increase the efficiency of the laser.
Use Quality Materials
Earlier it was difficult to cut thick material in a consistently smooth edge. Today, with the help of technology, it is easy to cut thick materials. But sometimes the edge quality gets compromised. To deal with this problem, using laser-quality, mill-scale materials is advisable. Quality materials will help to process thicker materials.
Use the Right File Format
In laser cutting .dxf or .dwg files are common. Hence, it is necessary to choose the correct file for better efficiency. Many software and applications are available that will help you. With the help of those you can convert PDF, .eps, .svg, and other file formats into .dxf or .dwg files.
Keep a Check on Spacing
When cutting multiple parts on the same metal sheet, spacing plays a significant role. If the parts are too close or you cut the features too thin then there is a risk of the burning down the material. Therefore, it is advisable to keep the appropriate spacing.
Better Nozzles
For machines to effectively cut thicker materials it is necessary to make advancements in cutting nozzles. For this, popular technologies like oxygen cutting, and nitrogen cutting are available. They have a high-powered ability to cut at high speeds in thin materials.
If you need help in increasing the efficiency of your machines, you can search for manufactures online. Manufacturers like Prima Optics and Fanuc parts use functions and methods that help to improve laser-cutting efficiency.
Updating to New Technology
Over the years the laser beam quality has improved thanks to new technology. One of the recent developments is a fiber laser. It has a lower maintenance cost, simple operation, and can cut the metal at a higher speed.
By adopting such technologies, you can make the cutting process simpler and quicker.
Now let’s discuss a few practical processes that increase the efficiency of laser-cutting.
Automatic focusing
The first step in metal cutting is to set the focus on the surface of the sheet. The laser focus varies depending on the material. Earlier manual focusing method was used which was replaced by auto-focusing due to advancement in technology. By using an auto-focusing function, machines can adjust the focus to a suitable position. You can even adjust it according to material type and thickness. This, in turn, increases the laser-cutting efficiency.
Concentrated Perforation
It is the processing technique of the laser-cutting machine. The cutting process using traditional perforation technology includes 2 stages:
• Perforation and cutting contour 1
• Perforation and cutting contour 2
While the concentrated perforation process aims at completing the perforation of all contours and then moving forward to the cutting process.
This method increases the length of the machine’s trajectory, avoids burning and adds up to the effectiveness of laser cutting.
Common Edge Cutting
When two parts have a common edge, you can separate them with the help of a single cut. This is known as common edge cutting. It offers the following benefits:
• Reduce the number of perforations
• Reduce the length of the cut
• Minimize material waste
• Save cutting gas
• This can significantly improve efficiency.
Automatic Edge Finding
With the help of automatic edge finding function, the machine can sense the angle of the sheet and the cutting process automatically adjusts itself to suit the position of the sheet. This will reduce work intensity; time consumed and improve the laser-cutting function.
Conclusion:
Efficient laser-cutting saves material, reduces waste and provides economic benefits as well. Technological advancements in the laser industry have given rise to methods and functions that help increase the competence of laser-cutting.
If you are an enterprise dealing in this space and require assistance, solutions by brands that offer Prima Optics, Fanuc Parts and other leading manufacturers can be fruitful.
Comments